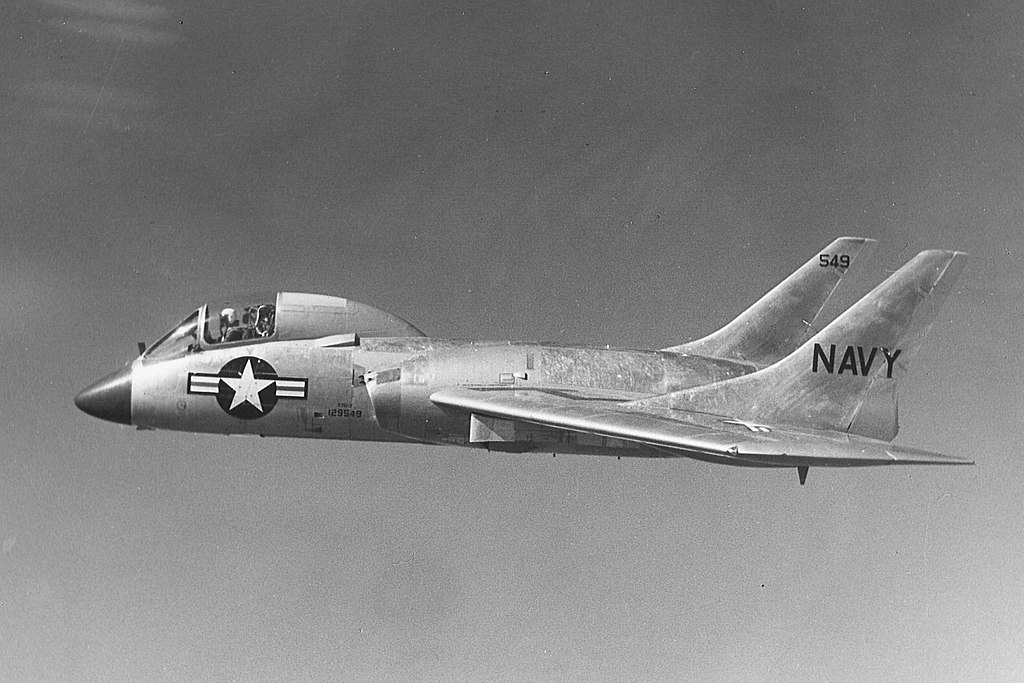
Chance Vought F7U Cutlass
Among the large amount of German aeronautical research data that began to reach the USA in the latter part of 1945, were details of some work on tailless designs carried out by Arado. These designs were developed by Chance Vought, leading to the production of the highly unconventional F7U Cutlass. The wing, with a sweepback of 38 degrees, was of very low aspect ratio, 3:1, and almost parallel chord. The pitch and roll controls were combined in elevons on the wing; the fins and rudders were located on the wing at the ends of the centre section.
Although its service career was relatively short-lived, the radical Chance Vought F7U Cutlass had a claim to fame on several counts. It was the first production aircraft to achieve supersonic flight, the first to release bombs at supersonic speed and, in its day, it was the heaviest single-seat carrier fighter in service with any navy. It also set the pattern for future generations of multi-mission combat aircraft, as it was readily adaptable as an interceptor, an air superiority fighter, a low-level attack aircraft or for day and night reconnaissance. But its loss rate was phenomenal. In 55,000 flying hours the Cutlass was involved in 78 accidents (21 of them fatal), resulting in an accident rate of 17 per 10,000 hours, compared with an average for US Navy combat types of 9.81.
The prototype XF7U-1 Cutlass first flew on 29 September 1948 and was followed by a pre-production batch of fourteen F7U-1s for service evaluation, the first of these flying on 1 March 1950. These aircraft were powered by a pair of Westinghouse J34-WE-32 turbojets developing a thrust of 3000 lb (4200 lb with reheat), and with these powerplants the F7U-1’s performance fell considerably short of US Navy requirements. The engines provided much less power than was needed to make the F7U safe to fly, much less a potent fighter. Poor engine thrust often resulted in the loss of aircraft. The F7U-1, in fact, was so underpowered that the pilot’s manual strictly forbade single engine approaches to carriers. Instead, the emergency instructions called for altitude, if possible, and ejecting, hopefully to safety. The Cutlass was simply too dangerous to risk a single-engine landing.
As serious as the lack of power was, a more serious design deficiency became manifest in the form of a weak drag link brace in the nose landing gear system. The unit frequently cracked during shipboard arrested landings, causing the nose gear to collapse violently. Since the aircraft was designed with a high angle of attack to produce more lift on take-off and landing, its nose dropped about 14 feet when the nose gear collapsed. Almost invariably, the pilot was critically injured or killed.
Chance Vought attempted to remedy the engine power problem by submitting proposals for a version with more powerful engines, the F7U-2, but this was doomed by the US defence cuts of 1949–50. Chance Vought nevertheless persevered with a much redesigned version, the F7U-3, and finally received a development contract in February 1950. Powered initially by two Allison J35-A-21 turbojets, the F7U-3 flew for the first time on 22 December 1951 and completed its carrier trials by July the following year. These trials demonstrated the Cutlass’s extraordinary low-speed handling characteristics, vindicating Chance Vought’s faith in their tailless configuration. The aircraft also proved to have good manoeuvrability and rate of climb. Nevertheless, it was still underpowered, and the new powerplant that had been selected for it, the Westinghouse J46, was slow to be delivered, with the result that the first F7U-3s did not reach the US Navy’s operational squadrons until late in 1954. Even then, the initially promising J46 design proved a disappointment. The J46 design promised 10,000 lb static dry thrust with reheat, but delivered less than half that. In addition, the engines had a relatively short life and needed a great deal of maintenance, with the result that much of the F7U fleet was non-operational for much of its seaborne deployment.
A further problem became apparent when the Cutlass’s guns were fired. The aircraft’s 20 mm cannon were mounted two on either side, just above the engine air intakes. Both engines had an alarming tendency to flame out when the guns were fired. Initially, the problem was thought to be caused by ingestion of gun gases, but was later proved to be the result of a pressure resonance phenomenon. When both sets of guns fired simultaneously, a pressure wave was created at the engine intakes. This pressure wave caused an organ pipe-type resonance, which then travelled to the aft section of the engine’s compressor, creating a stall condition. The resulting air mass led the compressor blades to overheat, perhaps causing the engine to either burn out, or disintegrate. The problem was later solved by installing circuits that prevented the left and right pairs of guns from firing simultaneously, but not before a number of aircraft and pilots were lost simply by firing their weapons at a target.
The first unit to equip with the Cutlass was US Navy Fighter Squadron VF-81, and a dozen other carrier-based squadrons also received the type. Early production F7U-3s were still somewhat underpowered, and most operational Cutlasses were re-engined with the more powerful J46-WE-8A turbojets when they became available. On 12 July 1955, a new Cutlass variant made its appearance; this was the F7U-3M, equipped with launching rails for four Sparrow I beam-riding anti-aircraft missiles and a ventral fuselage pack housing 2.75in Mighty Mouse folding fin aircraft rockets (FFAR). In March 1956, Attack Squadron VA-83, equipped with F7U-3Ms, became the first US Navy missile-armed squadron to deploy overseas, operating from the USS Intrepid as part of the US Sixth Fleet in the Mediterranean. Another version, the F7U-3P, also first flew in July 1955; this variant’s nose had been lengthened by just over two feet and was equipped with up to five cameras for day and night reconnaissance.
In the attack configuration, the Cutlass could carry an underwing load of up to 5400 lb. By the end of 1958, the F7U had been largely phased out in favour of more advanced types such as the F-8U Crusader, the last operational unit to use it being Attack Squadron VA-66.
Despite all its shortcomings, the Cutlass was popular with most pilots, once they got used to its idiosyncrasies. It was robust and could not be overstressed in high-g combat manoeuvres, and it could out-perform other navy combat aircraft of its era. Perhaps, when everything is taken into consideration, it did not really deserve the derogatory nickname of ‘Gutless’.
McDonnell F3H Demon
Another US Navy fighter that remained dangerously underpowered throughout its operational career was the McDonnell F3H Demon, so much so that it earned itself the nickname ‘Lead Sled’. Designed in response to a US Navy requirement for a carrier-based fighter with a performance comparable to that of land-based aircraft, the McDonnell XF3H-1 Demon flew for the first time on 7 August 1951, powered by the new Westinghouse XJ40-WE-6 turbojet, which proved to be extremely unreliable during flight testing. In August 1952, the first prototype was damaged in a landing accident following an in-flight engine failure. Both prototypes were temporarily grounded on two occasions because of engine problems. In addition, early flight testing revealed problems with poor forward visibility, an excessively slow roll rate, and inadequate lateral stability. A redesign of the nose section on production models cured the visibility problem. The roll rate problem was cured by moving the ailerons further inboard, with a corresponding decrease in the length and area of the trailing-edge flaps. The lateral stability was improved by removing the wing fence from each outboard wing panel.
The second prototype was fitted with a 10,500 lb thrust afterburning J40-WE-8 in January 1953. This engine did not prove to be any more reliable than the non-afterburning XJ40-WE-6. This aircraft was used for preliminary evaluation tests at the Naval Air Test Center (NATC) at Patuxent River, Maryland, beginning in August 1953. In October 1953, the second XF3H-1 was used for initial carrier trials aboard the USS Coral Sea (CVA-43). These trials were fairly successful, but there were some problems with low visibility during carrier approach and landing.
The first XF3H-1 was lost in a crash on 18 March 1954, following an in-flight engine explosion. The second prototype was permanently grounded shortly thereafter. It was later shipped to the Naval Air Development Center at Johnsville, Pennsylvania, to be used in barrier engagement tests.
Meanwhile, the US Navy had decided to place substantial production orders for two variants: the F3H-1N, to be built by McDonnell and powered by a 7500 lb thrust J40-WE-8, and the F3H-3, to be built by Temco and powered by the J40-WE-22. The F3H-1N was powered by the J40-WE-8 throughout its initial trials, but in its production form it was fitted with the J40-WE-22 or -22A engine, rated at 7500 lb thrust dry and 10,900 lb thrust with afterburning. Even with this engine, the F3H-1N was decidedly underpowered, and it was planned to replace the J40-WE-22 with the more powerful J40-WE-24 when it eventually became available.
By September 1953, it was apparent that the J40-WE-24 engine was never going to materialise, and the US Navy would have to be satisfied with the lower-thrust J40-WE-22. The first production F3H-1N took off on its maiden flight on 24 December 1953. The first few F3H-1Ns were intended for service evaluation and carrier suitability tests. In early 1954, the first F3H-1N was turned over for service evaluation at NATC Patuxent River in Maryland.
Production of the F3H-1N proceeded very slowly because of late deliveries of the J40-WE-22 engines. The US Navy service test programme immediately ran into serious trouble. Within the space of only a few days, no fewer than eleven accidents occurred, some of them fatal. Newspaper headlines and editorials screamed about the US Navy having acquired a dangerous and deadly aircraft, one that was more hazardous to its own pilots than to any potential enemy. Not only was the F3H-1N seriously underpowered, its powerplant was prone to in-flight explosions and sudden failures. Consequently, the F3H-1N was a completely unsafe aircraft, and was heartily disliked by its pilots. The problems with the engine proved to be incurable, and the US Navy was forced to call a halt to F3H-1N production after only fifty-eight examples had been built. Work on the F3H-1P photo-reconnaissance variant was stopped before anything could be built, and the contract with Temco was cancelled in its entirety. The US Navy permanently grounded all of its F3H-1Ns in July 1955. The F3H-1N debacle had cost the US Navy some $200 million, most of which had been spent on the unsuccessful J40-WE-22 engine.
The F3H-3 was cancelled altogether. The whole production line was held up until the more reliable Allison J71 turbojet became available, and it was with the J71 that the Demon finally became operational with US Navy Fighter Squadron VF-14 in March 1956. The first Demons to be assigned to the fleet were the F3H-2N night and all-weather fighter variant; further variants were the F3H-2M day fighter, armed with Sparrow missiles, and the F3H-2P photo-reconnaissance aircraft. The first Sparrow-armed F3H-2Ms were deployed with the Seventh Fleet in the Pacific late in 1958, the squadrons in question being VF-64 (USS Midway) and VF-193 (USS Bon Homme Richard). Twenty-nine of the F3H-2s delivered to the US Navy were in fact F3H-1s, updated and equipped with the J71 engine. One hundred and nineteen F3H-2 Demons were built before production ended in 1959 and the type remained in service until August 1964, the last F3H-3Ms (F-3Bs) retiring from VF-161.
Boeing B-47 Stratojet
In its efforts to assist the USAF Strategic Air Command (SAC) to build up a potent nuclear strike force in the 1950s, the American aviation industry produced some radical bomber designs, the first of which was the Boeing B-47 Stratojet. All had peculiarities that rendered them dangerous in certain situations, and in the case of the B-47 it was during take-off and landing that the bomber needed extremely careful handling.
The B-47 was a radical departure from conventional design. It featured a thin, flexible wing – based on German wartime research data – with 35 degrees of sweep and equipped with six turbojets in underwing pods, the main undercarriage being housed in the fuselage. It carried underwing fuel tanks, and was fitted with eighteen JATO (jet-assisted take-off) solid fuel rockets to give an emergency take-off thrust of up to 20,000 lb. These were not used during normal operational training, but would have been necessary in a real combat situation to get the B-47, carrying maximum fuel and a 10,000 lb bomb load, off the ground.
The B-47’s undercarriage consisted of two pairs of mainwheels mounted in tandem under the fuselage and outrigger wheels under each wing; the main gear folded up into the fuselage, while the outriggers retracted into the inboard engine nacelles. The arrangement was light and space-saving, but gave the B-47 a tendency to roll on take-off, so that in a strong crosswind the pilot had to hold the control column right over to one side. Steering on the ground was accomplished by the nosewheel, which was adjusted to prevent the aircraft swinging more than six degrees either way. However, the aircraft’s optimum attitude for take-off was the one it assumed as it sat on the ground, and at about 140 knots (depending on its weight), the Stratojet literally flew itself off the runway with no need for backward pressure on the control column. Once off the ground, with flaps up and the aircraft automatically trimmed, the technique was to hold it down until a safe flying speed had been reached and then climb at a shallow angle until 310 knots showed on the airspeed indicator. The rate of climb would then be increased to 4000 or 5000 feet per minute, depending on the aircraft’s configuration.
At its operating altitude of around 40,000 feet, the B-47 handled lightly and could easily be trimmed to fly hands-off. The quietness of the cockpit, the lack of vibration and the smoothness of the flight were noticeable, the only exception being when turbulence was encountered at high altitude in jet streams. Then, looking out of the cockpit, the crew could see the B-47’s long, flexible wings bending up and down – a rather unnerving phenomenon when experienced for the first time.
The B-47 had a spectacular landing technique that began with a long, straight-in approach from high altitude when the pilot lowered his undercarriage to act as an air brake; with its landing gear down the Stratojet was capable of losing 20,000 feet in four minutes. The flaps were not lowered until the final approach, which started several miles from the end of the runway and demanded great concentration. The bomber could not be allowed to stall, yet its speed had to be kept as low as was safely possible to prevent it from running off the far end of the runway. Each additional knot above the crucial landing speed added another 500 feet to the landing run, so the pilot had to fly to within two knots of the landing speed, which was usually about 130 knots for a light B-47 at the end of a sortie.
Ideally, the Stratojet pilot aimed to touch down on both tandem mainwheel units together, because if only one made contact with the runway first the aircraft bounced back into the air. With the wheels firmly down, the pilot used his ailerons to keep the wings level, much as a glider pilot does after touchdown, and as the ailerons were moved the flaps automatically adjusted their position to help counteract roll; the rudder had to be used very cautiously and sparingly or the aircraft might turn over. To slow the fast-rolling B-47, a brake parachute was deployed immediately on touchdown, and the pilot applied heavy braking. In addition, the aircraft was fitted with an anti-skid device that automatically released the brakes and then reapplied them to give fresh ‘bite’. On average, the B-47’s landing roll used up 7000 feet (1.3 miles) of runway.
What could happen if a B-47’s landing went disastrously wrong was demonstrated on 27 July 1956. A Stratojet went out of control while practising roller landings at RAF Lakenheath, Suffolk, and slid off the runway into the bomb dump. Its fuel tanks exploded, killing the crew, and the resultant fire enveloped a storage igloo containing several nuclear weapons in storage configuration, with no nuclear capsules present. The high-explosive (HE) elements in themselves might have caused a sizeable explosion, but the heat-and blast-resistant nature of the igloo prevented damage to the interior and the HE did not detonate. On another occasion, a B-47 was taking off with one nuclear weapon in strike configuration – in other words, with all components in place, but unarmed – when the aircraft’s port rear wheel casing failed at 30 knots. The Stratojet’s tail struck the runway and a fuel tank ruptured. The aircraft burned for seven hours after crash crews evacuated the area, ten minutes after the accident. The HE element of the weapon did not detonate, but the nuclear capsule was destroyed in the fire and some local contamination resulted.
The B-47 suffered many landing accidents during its career, and never quite lost its reputation as a crew-killer. Its mighty successor, the Boeing B-52 Stratofortress, also had problems in its early stages, although not with such disastrous results. The turbos had a tendency to explode, causing fires or wrecking sections of the fuselage, and the main undercarriage units were a constant source of trouble. On the ground the bomber rested on four twin-wheel units, all of which were steerable and could be slewed in unison to allow crosswind landings to be made with the wings level and the aircraft crabbing diagonally onto the runway; the trouble was that the main gear trucks had a habit of trying to slew in two different directions at the same time, or of jamming in the maximum 20degree slewed position. The bomber’s big Fowler-type flaps also had a tendency to crack and break under the tremendous sonic buffeting set up by full-power take-offs. Problems such as these caused the B-52 fleet to be grounded on several occasions before they were eventually solved, a process that took two years.
Convair B-58 Hustler
One of SAC’s biggest headaches, however, was caused by its most revolutionary bomber of the 1950s, the supersonic Convair B-58 Hustler, designed to replace the B-47. The B-58 originated from a 1949 USAF design study competition, which was won by the Fort Worth Division of Convair (General Dynamics). The design was given the designation B-58 in 1951, when Convair was awarded another contract to continue the study of the supersonic bombing concept, and in 1952 a third USAF contract gave the company the go-ahead to produce the B-58 as a viable weapons system. The aircraft was ordered into production in October 1954, and the prototype first flew on 11 November 1956. This was followed by a second prototype and a pre-production batch of eleven YB-58As for testing and evaluation.
The B-58 was a bold departure from conventional design. It had a delta wing with a conical-cambered leading edge, an area-ruled fuselage and four podded General Electric J79-GE-5B turbojets. The three-man crew were seated in tandem cockpits, and the B-58 was the first aircraft in the world in which the crew had individual escape capsules for use at supersonic speed. The aircraft had no internal weapons bay. Instead, it carried a large under-fuselage pod, housing weaponry, fuel, reconnaissance sensors and ECM equipment. Fuel was carried in the pod’s lower component, which could be jettisoned under combat conditions when its contents were exhausted. The upper part of the pod was also jettisoned after weapon release, leaving the aircraft aerodynamically clean for the flight out of the target area. The aircraft had a built-in defensive armament of a 20 mm rotary cannon in the extreme tail.
Even before the first B-58s were delivered to SAC’s operational squadrons, an alarmingly high accident rate had led to the type’s acceptance being delayed by the USAF. The first accident occurred on 16 December 1958, near Cannon AFB, New Mexico, when 58-0018 was lost. The accident was attributed to a loss of control during normal flight when the autotrim and ratio changer were rendered inoperative because of an electrical system failure. On 14 May 1959, 58-1012 was destroyed by fire during a refuelling operation at Carswell AFB. Another aircraft was destroyed on 16 September when a tyre blew during take-off from Carswell AFB, and on 27 October, 55-0669 was destroyed near Hattiesburg, Mississippi, when it lost control during normal flight. On 7 November, 55-0664 was destroyed during a high-speed test flight near Lawton, Oklahoma, when it disintegrated in mid-air, killing Convair test pilot Raymond Fitzgerald and flight engineer Donald A. Siedhof. On 22 April 1960 a failure of the Mach/airspeed/air data system caused the loss of 58-1023 near Hill AFB, Utah, and on 4 June 1960, 55-0667 was lost due to pilot error while flying at supersonic speed near Lubbock, Texas.
The first fully operational B-58A was delivered to the 43rd Bomb Wing at Carswell AFB on 1 August 1960, and in the spring of 1961 the 305th Bomb Wing at Bunker Hill, Indiana, also equipped with the type. The B-58’s career was relatively short-lived, the type being phased out in 1969. During that time the Hustler established several international records. However, even one of these attempts ended in tragedy when, on 3 June 1961, B-58 59-2451 crashed after taking off from Le Bourget, Paris, after a record-breaking eastbound transatlantic flight. All three crew were killed.
Of the 116 B-58s built, 26 were destroyed in accidents, mostly during the test and evaluation phase. Others were so badly damaged that they could not be returned to service. It would be twenty years before the USAF received a supersonic strategic bomber on which it could really depend, the Rockwell B-1.