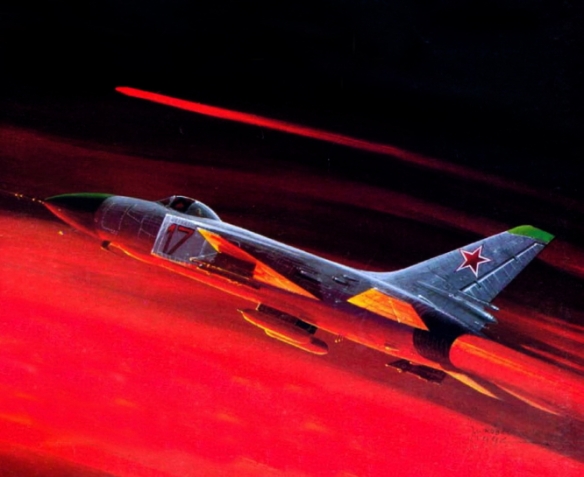
In the 1950s the Moscow-based Central Aero and Hydrodynamics Institute (CAHI, often rendered as TsAGI) had refined a configuration for Mach-2 aircraft with a triangular delta wing and swept tailplanes. This shape was used by Mikoyan for the MiG-21 family, and by Sukhoi for the significantly larger Su-9 all-weather interceptor. By 1962 this had been developed into the Su-11, with a more powerful radar and better missiles. By this time the Sukhoi bureau was working on a much more powerful twin-engined design, the T-58, which matured as the Su-15. Production aircraft followed the Yak-28P at Novosibirsk, the final batches being of the Su-15TM version with R13-300 engines, later radar and additional weapon options including externally hung UPK-23-250 gun pods. Called ‘Flagon’ by NATO, these attractive aircraft had a wing extended in span to just over 30 feet, but a fuselage no less than 69 feet long. They achieved the rare distinction of shooting down unidentified targets that turned out to be civil airliners that had strayed far from their authorised track: a 707 on 20 April 1978 and a 747 on 1 September 1983, both of Korean Air Lines.
The Su-15 is a single-seat supersonic interceptor designed for day and night VMC/IMC operations. The all-metal airframe is made mostly of D-16 duralumin, V95 and AK4-1 aluminium alloys; highly stressed parts are made of 30KhGSA, 30KhGSNA and 30KhGSL grade steel, while parts of the rear fuselage structure subjected to high temperatures are made of OT4- titanium alloy.
The fuselage is a semi-monocoque riveted stressed-skin structure whose crosssection changes from circular (in the forward fuselage) to almost rectangular (in the area of the air intakes) to elliptical with the longer axis horizontal (in the rear fuselage). It is built in two sections, with a break point at frames 34/35 allowing the rear fuselage to be detached for engine maintenance and removal; the two fuselage sections are held together by bolts. The forward fuselage (Section F-1) includes the radome, the pressurised cockpit, two avionics/equipment bays fore and aft of it, the nosewheel well under the cockpit, the air intake assemblies and inlet ducts, the engine bays and the fuel tank bays. The detachable GRP radome tipped with the main air data boom has a simple conical shape on the Su-15/Su-15T/Su-15U and an ogival shape on the Su-15TM/Su-15UT.
The forward avionics bay (frames 1-4) houses the radar set. On single-seat versions the cockpit is contained by pressure bulkheads at frames 4 and 14A and enclosed by a two-piece teardrop canopy. The fixed windshield features curved triangular Perspex sidelights and an elliptical optically-flat bulletproof windscreen made of silicate glass; the aft-sliding canopy portion with blown Perspex glazing can be jettisoned manually or pyrotechnically in an emergency. The Su-15UT trainer features a longer forward fuselage; the tandem cockpits enclosed by a common four-piece canopy with individual aft-hinged sections over the two seats. In contrast, the Su-15UM trainer does not have a fuselage stretch, being dimensionally identical to the single seat Su-15TM.
The forward fuselage is area-ruled, starting at the cockpit section which is flanked by the air intakes. The air intake trunks are rectangular-section structures blending into the centre portion of the fuselage. The intakes have sharp lips and are provided with boundary layer splitter plates which are attached to the fuselage by V-shaped fairings spilling the boundary layer. To improve performance at high angles of attack the air intake trunks are canted outward 2°30’. Each intake features a three-segment vertical airflow control ramp and a rectangular auxiliary blow-in door on the outer side; these are governed by the UVD-58M engine/intake control system. The centre portion (frames 14A-34) accommodates three integral fuel tanks, the inlet ducts, whose cross-section gradually changes to circular, and the engine bays (frames 28-34); it features two ‘wet’ external stores hard-points side by side. Titanium firewalls and heat shields are provided in the engine bays to contain possible fires. The rear fuselage (Section F-2) carries the tail surfaces and a detachable ‘pen nib’ fairing made of titanium and stainless steel sheet between the engine nozzles; it accommodates the engine jetpipes and the tailplane actuators. Four airbrakes with a total area of 1.32 m2 (14.19 sq ft) are located between frames 3538, opening 50°.
The cantilever mid-set wings are of simple delta shape with 60° leading-edge sweep on the Su-15 sans suffixe, with 2° anhedral and zero incidence. The Su-15T and Su-15TM have increased-area wings with a leading-edge kink at 2.625 m (8 ft 7⅜ in) from the centreline, the outer portions featuring 45° leading-edge sweep and 7° negative camber. The wings are one-piece structures of two-spar stressed-skin construction joined to the fuselage at mainframes 16, 21, 25, 28 and 29. On the pure delta version each wing has 17 ribs, 28 rib caps and three auxiliary spars which, together with the front and rear spars, form five bays: the leading edge, forward bay, mainwheel well (between the Nos. 1 and 2 auxiliary spars), rear bay and trailing edge. The double-delta versions have 18 ribs and 29 rib caps per wing. The bays between the Nos. 2 and 3 auxiliary spars are integral fuel tanks whose skin panels are stamped integrally with the ribs and stringers; ordinary sheet metal skins are used elsewhere. Each wing has a single boundary layer fence on the upper side. The wings have one-piece blown flaps, with one-piece ailerons outboard of these. The flaps are hydraulically actuated, with pneumatic extension in an emergency; flap settings are 15° for take-off and 25° for landing when the BLCS is on, or 25° and 45° respectively with the BLCS off. The ailerons are aerodynamically balanced and mass-balanced, with a travel limit of ±18°30’. There are two external stores hardpoints on each wing.
The conventional tail surfaces swept back 55° at quarter-chord are of riveted stressed-skin construction. The vertical tail comprises a one-piece fin an inset rudder. The fin is a single-spar structure attached to fuselage mainframes 35 and 42, with a rear auxiliary spar (internal brace), front and rear false spars, stringers and ribs; it features a root fillet and a glassfibre tip fairing. The mass-balanced rudder is a single-spar structure; it is carried on three brackets. The cantilever horizontal tail mounted 110 mm (4⅜ in) below the fuselage waterline consists of differentially movable slab stabilisers (stabilators) turning on stub axles attached to fuselage mainframe 43; anhedral 2°, incidence in neutral position –4°10’. Each stabilator is a single-spar structure with front and rear false spars, stringers and ribs, and sheet duralumin skins. The stabilators feature anti-flutter booms angled 15° upwards at the tips.
The tricycle landing gear is hydraulically retractable, with pneumatic emergency extension; all units have levered suspension and oleo-pneumatic shock absorbers. The forward-retracting nose unit is equipped with a shimmy damper, castoring through ±60°; steering on the ground is by differential braking. On the Su-15 sans suffixe the nose unit has a single 660 x 200 mm (26.0 x 7.87 in) KT-61/3 wheel (koleso tormoznoye – brake wheel). The Su-15T, Su-15TM and Su-15UM have a taller nose gear unit with twin 620 x 180 mm (24.4 x 7.0 in) KN-9 wheels (koleso netormoznoye – non-braking wheel). The main units retracting inward into the wing roots are equipped with 880 x 230 mm (34.6 x 9.0 in) KT-117 brake wheels on all versions. All brake wheels feature pneumatically actuated disc brakes. The nosewheel well is closed by clamshell doors, the mainwheel wells by triple doors (one segment is hinged to the front spar, one to the root rib and a third segment attached to the strut); all doors remain open when the gear is down. A PT-15 ribbon-type brake parachute with an area of 25 m2 (268.8 sq ft) housed in a fairing at the base of the fin is provided to shorten the landing run.