August 2014 the US Navy awarded the contract to build the first production Ship-to-Shore Connector (SSC). The LCAC 101 is the first of 72 operational craft to be delivered from August 2017, with a targeted initial operational capability in 2020. The test and training craft is expected to start construction by November 2014.
The Ship to Shore Connector (SSC) is the functional replacement for the existing fleet of Landing Craft, Air Cushioned (LCAC) vehicles, which are nearing the end of their service life. The SSC is an air-cushioned landing craft intended to transport personnel, weapon systems, equipment, and cargo from amphibious vessels to shore. The vessel can rapidly move assault forces to conduct amphibious operations and operate over the high water mark to include movements over ice, mud, and swamps.
Mission: Transports vehicles, heavy equipment, and supplies through varied environmental conditions from amphibious ships to shore. Enhances the Navy and Marine Corps capability to execute a broad spectrum of missions from humanitarian assistance and disaster response to multidimensional amphibious assault.
Prime Contractor: Textron Incorporated; New Orleans, LA
End of August, 2014 the Naval Sea Systems Command awarded a contract modification for the construction of the US Navy’s first production-standard ship-to-shore connector (SSC). Landing Craft Air Cushion (LCAC – pronounce L-cac)101 is the second craft in the SSC class. It was designed as an evolutionary replacement of currently ageing fleet of LCACs, for which a service life extension programme is underway.
The industrial team led by Textron which includes aluminium manufacturer Alcoa Defense and command, control, computers, communications and navigation specialist L-3 Communications, is today working on the detailed design and construction of the SSC test and training craft (LCAC 100), which is to be delivered in February 2017. The 101 is the first of 72, with an initial operational capability targeted for 2020. Although it externally resembles the current type, the new craft includes enhancements driven by design service life extended to 30 years sans service life extension programme, increased payload capacities thanks to two, instead of four but new more powerful, Rolls-RoyceMT7turbine engines(the type is derivative of the Osprey tiltrotor aircraft), reduced flight crew and workload, increased reliability and maintainability.
The SSC will be able to carry a load of 74 tonnes – say an Abrams – in Sea State 3 at a speed of more than 40 knots to a shore some from 25 nm away. The US Navy is also planning to begin the procurement of a new Surface Connector (X) Replacement – SC(X)R – in Fiscal Year 2018, to replace the ageing Landing Craft Utility (LCU) 1610 fleet. A so-called Analysis of Alternative completed in the first half of 2014 favoured a low-risk evolution of the LCU design to replace the current 32 1610s on a one-to-one basis. Nevertheless the US Navy and Marine Corps are studying concepts to bridge the ship-to-shore connector gap in the coming years.
#
The Ship to Shore Connector (SSC) is the evolutionary replacement for the existing fleet of Landing Craft, Air Cushion (LCAC) vehicles, which are nearing the end of their service life. The SSC is an air cushion vehicle whose mission is to land surface assault elements in support of Operational Maneuver from the Sea (OMFTS), at over-the-horizon distances, while operating from amphibious ships and mobile landing platforms. SSC provides increased performance to handle current and future missions, as well as improvements which will increase craft availability and reduce total ownership cost.
The SSC program will significantly enhance the Navy and Marine Corps team’s capability to execute a broad spectrum of missions well into the 21st century, from humanitarian assistance and disaster response to multidimensional amphibious assault. LCACs/SSCs are used primarily to haul vehicles, heavy equipment, and supplies through varied environmental conditions from amphibious ships to over the beach.
Additionally, an enclosed personnel transport module can be loaded aboard that can hold up to 180 passengers or 54 casualty personnel. LCACs have proven to be very useful in supporting non-hostile amphibious operations and were vital in delivering life-saving equipment, food, water, and medical supplies in humanitarian relief efforts throughout the world. It is anticipated that SSC will be called upon to perform in a similar manner.
The SSC program is the first major naval acquisition program in more than 15 years to be designed “in-house” by the Navy rather than by private industry. The Navy design team progressed through an evolutionary design process, beginning with a set-based design process, where craft level requirements were functionally decomposed into discrete system level functional requirements documents (FRDs). The FRDs formed the functional basis for selecting trade spaces, and to start Preliminary Design. Preliminary Design was followed by a Contract Design period, which developed the Allocated Baseline and formed the basis for the SSC contract solicitation.
The Navy-led contract design, released to industry in a full and open competition, allowed for mid-tier builders without air cushioned vehicle experience to compete for the detail design and construction contract. This approach uses the government’s expertise in air cushioned vehicles and provides industry the flexibility to make component selections and complete design details for optimal producibility and low acquisition costs.
The Detail, Design and Construction (DD&C) contract was awarded to Textron, Inc., New Orleans, LA., whose major subcontractors are L-3 Communications of Camden, NJ, GE Dowty of Great Britain, Rolls-Royce Naval Marine of Indianapolis, IN, Innovative Power Solutions of Eatontown, Meritor, Inc of Troy, MI, and Umoe Mandal of Norway. Other subcontractors include Marvin Land Systems of Inglewood, CA, Donaldson Company, Inc. of Minneapolis, MN, Exlar Corporation of Chanhassen, MA, Advanced Composite Products & Technology of Huntington Beach, CA, Supreme Integrated Technology of Harahan, LA, and Technology Dynamics, Inc. of Bergenfield, New Jersey.
The SSC Program of Record is for a total of 73 craft (one Test and Training and 72 operational craft). Deliveries will begin in fiscal year 2019 with initial operational capability projected for fiscal year 2020.
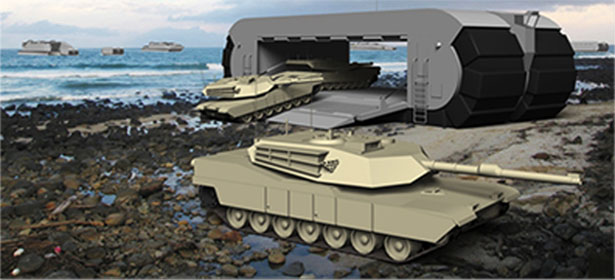
Full scale version concept art – UHAC
During the Advanced Warfighting Experiment in conjunction with the Rimpac C 2014 multinational exercise lead by US Forces, the US Marine Corps tested the half scale prototype of the UHAC currently under development.
During the Advanced Warfighting Experiment in conjunction with the Rimpac 2014 multinational exercise led by the US Forces, the Marine Corps tested the half-scale prototype of the Ultra Heavy-lift Amphibious Connector(UHAC). Funded by the Office of Naval Research and built by Navatek, a full-scale craft is expected to carry three times the payload of an LCAC and beat 10-foot high sea walls.
So, what is the full-scale version of this vehicle capable of? Well it can power across water with a payload of 2000 tons at a speed of 20 knots i.e. 37 kilometers per hour. It can even drive up on to the shore and over obstructions which can be as high as 10 feet!
After successfully achieving the goals of a half-scale prototype, the US Marines are all set to boast triple the carrying capacity of the Landing Craft Air Cushion (LCAC) vehicles that are currently used to transport from ship-to-shore for the US Navy by providing a payload of 190 tons. As far as the dimensions are concerned, the vehicle is 8 meters wide, 13 meters long, and 5 meters high.
The vehicle is a modification of the Captive Air Amphibious Transport (CAAT) concept. The UHAC is capable of moving on sea as well as land. It is fitted with captured-air foam cells that provide buoyancy which in turn act as paddles in water whereas it acts as track-driven pads on land. What makes the ‘A’ in UHAC is the ability of the system to apply minimal ground pressure footprint.
Navatek Ltd, a hydrodynamic research and naval architecture company in Honolulu, created the project, and as for the its sponsorship and execution is concerned, the Office of Naval Research (ONR) was responsible. Rim of the Pacific aka RIMPAC is currently the world’s largest international maritime warfare exercise which runs from June to July after every two years. The US invite military forces from the Pacific Rim to come to the Hawaiian Islands to participate.